Wczesne próby zrozumienia linii montażowej
Pierwsi badacze pojawili się tam, gdzie pracował tłum robotników. Zastanawiali się, dlaczego część osób radzi sobie szybciej, a inni zostają w tyle. Obserwowali ułożenie maszyn i trasy wózków transportowych. W tamtych czasach brakowało zaawansowanych metod analizy. Wiele spostrzeżeń pochodziło z cierpliwych obserwacji i długich rozmów z robotnikami. Sprawdzano, czy warto zmienić ustawienie prasy albo wydłużyć stół roboczy. Eksperymentowano z drobnymi usprawnieniami, nie zawsze trafionymi. Człowiek zaczął zapisywać czasy operacji i przeliczać je na wykresach. Powstały pierwsze koncepcje przepływu pracy, rozplanowania stanowisk i eliminowania zbędnych ruchów. Niewiele osób doceniało wówczas te starania, ale to właśnie one zasiały ziarno przyszłych wielkich zmian w fabrykach.
Rola obliczeń w optymalizacji produkcji
Nauka nie ogranicza się tylko do mechaniki czy chemii. W optymalizacji produkcji ogromną wagę ma również matematyka. Statystycy odkryli, że nawet drobne różnice w tempie pracy przekładają się na wielkie różnice w wynikach. Analiza wartości średnich i odchyleń zaczęła wskazywać miejsca, gdzie pojawiają się tak zwane wąskie gardła. Dzięki temu produkcja mogła być bardziej przewidywalna. Menedżerowie wiedzieli, ile materiału przygotować na kolejny tydzień i w jaki sposób podzielić pracę między poszczególne linie. Gdy pojawiał się przestój, statystyki podpowiadały, czy to wina niewłaściwego planowania czy może awarii urządzenia.
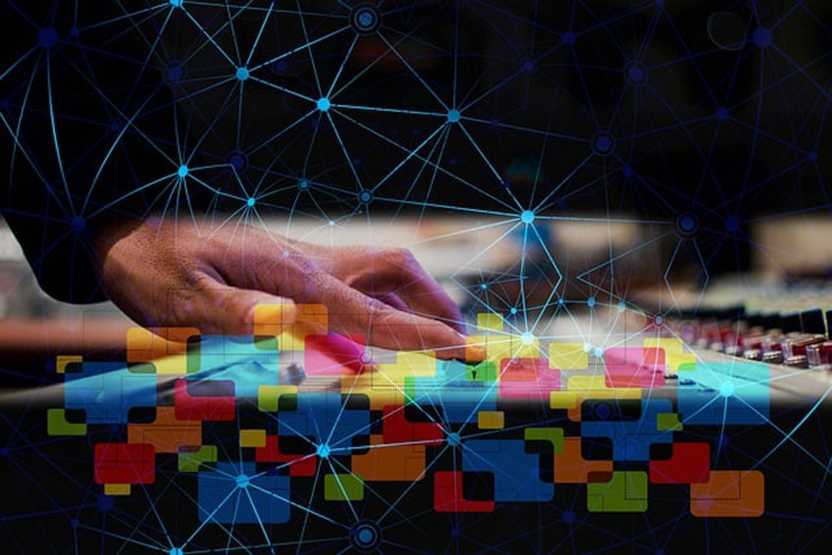
Badania operacyjne i poszukiwanie optymalnego wyniku
Nagle więc w większych fabrykach zaroiło się od zespołów inżynierów i matematyków. Tworzyli modele, które miały opisać procesy wytwórcze za pomocą równań i funkcji. Pojawiła się dziedzina zwana badaniami operacyjnymi. Jej celem było znalezienie strategii, która minimalizuje koszty i maksymalizuje wydajność. Metody liniowe, programowanie całkowitoliczbowe i sieci przepływów stały się narzędziami codziennej pracy. Na ekranach komputerów inżynierowie oglądali symulacje, w których dziesiątki tysięcy możliwych konfiguracji maszyn były sprawdzane w poszukiwaniu tej jednej, dającej najlepszy efekt. To wyglądało niczym laboratorium w wirtualnej rzeczywistości. Planowanie produkcji, które dawniej opierało się na intuicji, zaczynało więc korzystać z mocy obliczeniowej komputerów. Można było z góry przewidzieć, co stanie się przy wzroście popytu, albo jak rozdzielić zasoby, by uniknąć przestojów. To był krok milowy w stronę świadomego zarządzania.
Środowiska symulacyjne i komputerowe modele
Dziś naukowcy idą jeszcze dalej. Nie wystarcza im zwykłe liczenie na papierze. Jak widać według danych zamieszczonych na portalu naukowo – technicznym NIS, coraz częściej chcą oni mieć wirtualne odwzorowanie fabryki. Tak powstają komputerowe modele odzwierciedlające każdą linię produkcyjną, każdy surowiec i każdy ruch maszyny. W takim środowisku można zasymulować wprowadzenie nowych rozwiązań bez ryzyka realnych strat. Pracownik widzi na ekranie pulpit, który pokazuje układ zakładu. Jeśli zmieni czas realizacji jednej operacji, program natychmiast wyświetla skutki dla reszty procesu. Można wprowadzić różne scenariusze: brak prądu, nagły wzrost zamówień, częściowa awaria urządzenia. Dzięki temu da się szybko opracować procedury zapasowe i obniżyć ryzyko przestojów. Optymalizacja produkcji związana jest również z tym, że maszyny potrafią przewidywać, kiedy dany komponent się zużyje i zasugerować wymianę z wyprzedzeniem. Sieci neuronowe analizują setki parametrów równocześnie. Wypatrują drgań, zmian temperatury czy poziomu wibracji w maszynach. Dzięki temu można odkryć, że jakaś część silnika pracuje w sposób odbiegający od normy. Algorytm potrafi nawet podpowiedzieć, ile czasu zostało do momentu potencjalnej awarii. Zamiast więc czekać, aż coś się zepsuje, można zaplanować przerwę na remont w dogodnym terminie. To oszczędza środki i zapobiega nagłym przerwom w dostawach towaru.
Optymalizacja logistyki i zarządzanie łańcuchem dostaw
Optymalizacja produkcji nie kończy swojego działania w granicach fabryki. Jak zauważono w miesięczniku naukowo – technicznym, produkcja łączy się z logistyką, bo wytworzone dobra trzeba przemieszczać do magazynów i sklepów. Tu także wkracza precyzyjna analiza i poszukiwanie najlepszych tras. Specjaliści ds. transportu korzystają z teorii grafów i algorytmów wyznaczających najkrótsze drogi. Komputery biorą pod uwagę natężenie ruchu, koszty paliwa, a nawet zmienne warunki atmosferyczne. Dzięki temu załadunek i rozładunek przebiegają według harmonogramu, który jest stale aktualizowany. Kolejny krok stanowi łączenie łańcuchów dostaw w globalną sieć. Dostawca surowca ma dostęp do systemu, w którym widzi stany magazynowe odbiorcy. Może więc na bieżąco planować wysyłki i unikać sytuacji, w której fabryka musi czekać na spóźnioną dostawę. Dzięki temu cały proces od wydobycia surowca po finalny produkt nabiera płynności.
Rola człowieka w optymalizacji produkcji
Niektórzy obawiają się, że w przyszłości, w fabrykach zabraknie miejsca dla człowieka. W końcu maszyny przejmują coraz więcej zadań. Jednak wiadome jest, że bez specjalistów z zakresu analizy i planowania, cały ten mechanizm przestałby istnieć. Człowiek wciąż pozostaje kreatorem nowych pomysłów. To on definiuje wyzwania i parametry, które chcemy ulepszyć. Komputery działają sprawnie, ale wąska dziedzina wymaga ludzkiej wyobraźni, by wyjść poza dotychczasowe schematy. Naukowcy wspierają personel w firmach, pokazując nowe narzędzia i ucząc interpretacji danych. Dzięki temu każdy pracownik może stać się małym badaczem, który w swojej dziedzinie proponuje innowacje. Taki kolektywny wysiłek pozwala na nieustanne podnoszenie poziomu.
Spojrzenie w przyszłość związane z optymalizacją produkcji
Obecnie, minikomputery i czujniki pojawiają się w tak wielu miejscach, że trudno je policzyć. Każdy drobny element zbiera informacje o temperaturze, wilgotności czy wibracjach. Analiza tych danych wymaga zaawansowanych algorytmów, a te rodzą się w głowach matematyków i programistów. Nietrudno wyobrazić sobie świat, w którym produkcja jest niemal całkowicie zautomatyzowana, a nadzór sprawują inteligentne systemy analityczne. Ludzie, w dalszym ciągu będą jednak potrzebni, by tworzyć wizje nowych wyrobów i wyznaczać kierunki rozwoju. To nasza kreatywność i zdolność do stawiania pytań sprawiają, że rozwój nie stoi w miejscu.
Naukowe spojrzenie na produkcję pozwala wytyczać nowe szlaki. Dzięki temu fabryki milkną w miejscach, gdzie kiedyś huczały maszyny. A tam, gdzie dawniej panował chaos, dziś króluje przemyślana optymalizacja, która zmienia zwykłą pracę w pełen dynamizmu spektakl.
Napisz komentarz
Komentarze